Embarking on the Journey of Monoclonal Antibody (mAbs) Production
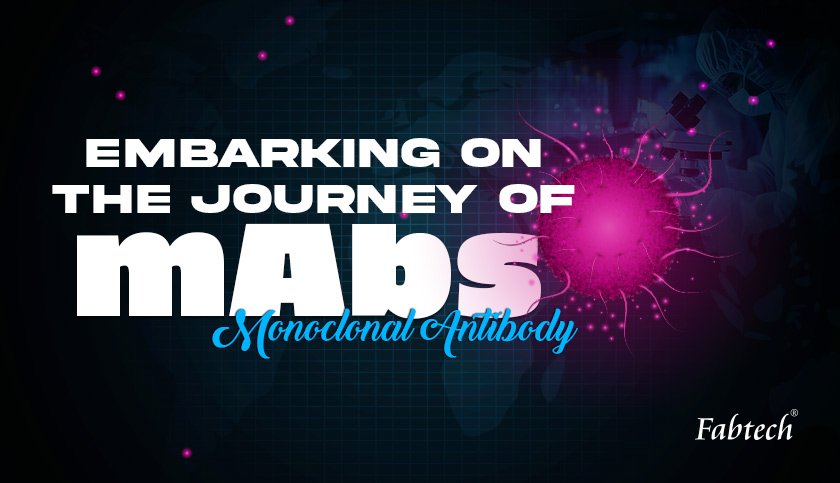
Antibodies are vital proteins present in the human body that help us fight infections. These antibodies circulate throughout the body, seeking out and binding to a specific protein called an antigen. Once attached, antibodies facilitate the destruction of cells containing the antigen, thereby strengthening the immune system response.
Advancements in technology and research now enable scientists to design antibodies that are not naturally found in the body. These engineered antibodies, called Monoclonal Antibodies (mAbs) target specific antigens to treat various diseases, including some types of cancer.
Essentially, mAbs mimic the actions of natural antibodies by attaching to specific targets on cancer cells and obstructing their function.
In recent years, mAb products have emerged as leaders in the biotherapeutics market. Hundreds of novel mAbs and mAb-like proteins are currently undergoing clinical development for the treatment of diseases in multiple therapeutic areas, including hematology, immunology, oncology, and infectious diseases.
This rise of mAbs signifies a significant transformation in modern medicine, with ongoing improvements in antibody engineering and a deeper understanding of their immunomodulatory properties. To meet the evolving demands of mAb production, Fabtech with its design and build expertise, offers efficient pharmaceutical engineering solutions crucial for achieving excellence in mAb production.
Quality by Design (QbD):
Quality by Design (QbD) serves as our structured approach to product development, ensuring consistent product quality, safety, and efficacy in manufacturing protocols. Leveraging comprehensive knowledge of antibody structure and function, combined with vast expertise in biopharmaceutical protein manufacturing processes, empowers the effective implementation of QbD in developing innovative therapeutic mAbs.
Antibody Engineering:
Our engineering solutions incorporate leading antibody engineering technologies to enhance the development of therapeutic antibody drugs, such as humanization of monoclonal antibodies, phage display, humanized antibody mouse, single B cell antibody technology, affinity maturation and hybridoma methods. These techniques aim at producing highly specific and effective mAbs, with optimal processing, stability, and tolerance.
Cell Line Development:
Cell line development involves generating and selecting highly productive cell lines while optimizing cell culture process conditions. This platform typically consists of a common host cell, expression vector, transfection, and selection methods during cell line generation, standard cell culture media, process control, and scale-up methodologies during process optimization.
Our approach enables fast process development, balanced productivity, controlled product quality, and process consistency across all stages and production scales.
Upstream and Downstream Processing:
Identifying and isolating antibody-producing cells and their further purification involves a continuous fluid transfer process. This stage, known as the upstream and downstream processing, demands stringent aseptic conditions to prevent contamination.
Product sterility becomes even more critical in the final step of mAbs filling, upon which the success of the manufacturing process depends. Fabtech’s aseptic filling solutions play an instrumental role in meeting the most rigorous quality standards of pharmaceutical facilities.
Analytical Techniques:
An array of analytical techniques such as mass spectrometry and liquid chromatography is required to characterize a monoclonal antibody fully. These characterization processes (physiochemical, structural, immunological, functional) strictly adhere to the guidelines of ICH and EMA to guarantee product quality, safety, and stability, thus enabling the smooth release of the biopharmaceutical drug in the market.
Facility Setup Considerations
Design for Flexibility:
The mAbs manufacturing platform for producing clinical material must demonstrate consistent performance across final product batches while meeting GMP. Fabtech ensures flexibility in the system for a seamless transition between products, scalability, and rapid production, particularly in the case of emerging infectious diseases. This adaptability to evolving biopharmaceutical landscapes, along with accommodating process changes, and technological advancements serves to future-proof the facility.
Quality Control Laboratories:
Establishing robust labs equipped with cutting-edge instrumentation and skilled personnel is essential for continually monitoring product quality. Monoclonal antibodies (mAbs) are delicate proteins that require precise temperature control and aseptic conditions during filling to maintain integrity.
Aseptic operations and sterile filtrations are essential in mAb production to prevent microbial contamination. Fabtech’s filling capping machines ensure sterile conditions, and are seamlessly integrated with formulation, filtration, and purification processes, eliminating contamination risks associated with manual handling.
Our purified water systems include Water for Injection (WFI) generation systems that serve as a reconstitution solvent in powdered vial mAb formulations, playing a critical role as a buffering agent to maintain pH and stability. It provides pyrogen-free water, which is indispensable for stability and helps minimize adverse reactions at the injection site.
Cleanroom Systems:
Fabtech has a long-standing track record in establishing sterile environments and offering clean air solutions that adhere to regulatory standards. Our expertise includes implementing features of HEPA filters for laminar airflow, which is instrumental in achieving impeccable monoclonal antibody (mAb) production.
Additionally, our process utilities, including heating, ventilation, and air conditioning HVAC systems, play a fundamental role in mitigating process-related impurities. This efficient approach minimizes the risk of contamination among personnel, from the environment, and prevents cross-contamination with other products.
Automation and Integration:
Unlike manual production, which involves overwhelming amounts of tissue culture and liquid handling steps to achieve high-throughput operation, automated systems can manage the required numbers of reagents more effectively.
A well-established and defined protocol or standard operating procedure (SOP) forms the basis for automating each task. This platform is compatible with enhancing efficiency and minimizing errors across bioreactor controls and purification processes.
Regulatory Compliance:
Ensuring compliance with Good Manufacturing Practices guidelines for pharmaceuticals (cGMP) and regulatory standards is essential to guarantee the safety and efficacy of mAb products, including conducting cleaning validations. Developing multiple mAb products presents unique regulatory considerations. Ensuring comparability between manufacturing processes allows one product to support another’s development.
Processes based on a platform approach are validated for specific products and sites, with product-specific control strategies. Safety, quantity, potency, identity, and purity tests are required for all mAb products during clinical development. Upper limits for impurities are established and supported by safety data. All batches must meet specifications for substance(s) and product, ensuring consistent quality as per GMP guidelines.
The ever-growing demand for mAbs production has underscored the importance of its associated factors in ensuring successful outcomes. Mastering the intricacies of monoclonal antibody (mAbs) production is crucial. This level of expertise is attainable through a blend of technical proficiency and meticulous facility design.
Embracing scientific advancements and technology, coupled with skilled personnel and ongoing product quality monitoring, positions Fabtech’s mAb production solution as a catalyst for pharmaceutical engineering projects to remain at the forefront of the industry.
To enhance the efficiency of your monoclonal antibody (mAB) production, partner with Fabtech, a leading biopharmaceutical engineering company specializing in the production of high-quality mAB products.
Categories
Recent Posts
Subscribe
Never miss a post from Fabtech. Sign up to receive updates direct to your inbox.