Fabtech’s Approach to Greenfield and Brownfield Projects
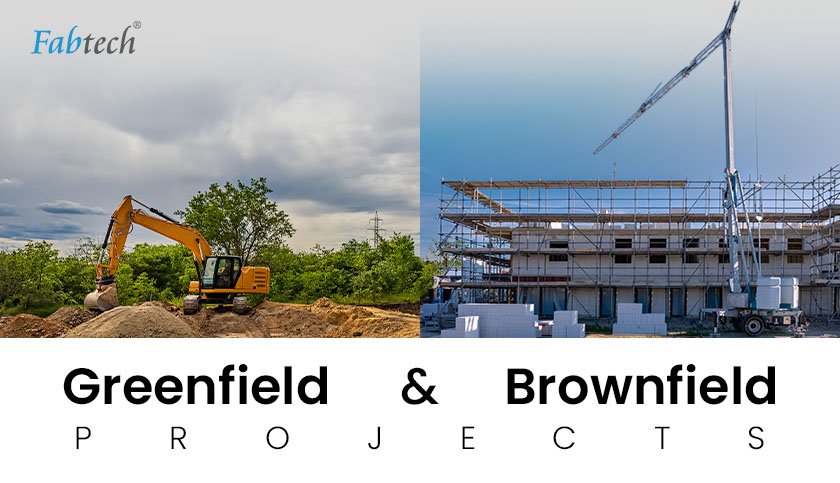
Being adaptive in one’s approach is vital to taking on new challenges and seizing opportunities. This flexibility becomes more important when managing diverse pharmaceutical engineering projects. Whether it’s building a new facility from scratch or upgrading an existing one, Fabtech offers specialised engineering solutions tailored to the unique needs of Greenfield and Brownfield projects. While a few core principles remain constant, the approach and execution strategies vary significantly. Both project types demand precision, innovation, and technical depth, but through different lenses.
Fabtech’s strength lies in understanding these differences and adapting accordingly.
Our Greenfield Project Capabilities: Building from the Ground Up
Greenfield projects offer a blank slate to design and build a facility from scratch, with full control over layout planning, utility placement, workflow optimisation, and the implementation of cutting-edge technologies. Fabtech leverages this opportunity to deliver advanced facilities engineered for future readiness and regulatory excellence.
Site Evaluation and Feasibility
Our process begins with comprehensive site evaluations and feasibility studies. We assess environmental factors such as air and water quality, potential noise pollution, and ecological impact while ensuring compliance with zoning laws, building codes, and regulatory frameworks. Logistical considerations like access routes, material movement, and storage capacity are also thoroughly examined.
Concept to Commissioning
Fabtech manages the entire lifecycle of the project. Our turnkey capabilities encompass basic and detailed design, procurement, construction, installation, validation, and handover. We ensure all systems are operationally ready before delivery.
1. Regulatory-Driven Design
Obtaining the necessary permits and approvals from various government bodies is a critical step. Fabtech integrates global standards, including good manufacturing practices guidelines for pharmaceuticals, USFDA, EMA, and WHO guidelines, into the facility blueprint from day one and handles permits and approvals with precision.
2. Future-Proof Infrastructure
Greenfield projects are designed to accommodate future expansions. We adopt modular layouts that allow for scalability, sustainability, and adaptability to evolving technologies and regulations. This includes using sustainable materials and planning for potential future impacts like climate change.
3. Optimised Utilities and Systems
The freedom of design allows us to optimise material and personnel flow, HVAC zoning, modular cleanroom systems, energy-efficient utilities and renewable integration. These solutions work in synergy to deliver high efficiency, productivity and operational excellence, resulting in a high-performance, GMP-compliant facility ready for future demands.
Our Brownfield Project Expertise: Transforming the Old into the New
Brownfield projects are about transformation. They involve expanding or upgrading existing facilities while minimising disruptions and maintaining ongoing pharma production. Fabtech works within the boundaries of such existing operations with precision, agility, and an in-depth understanding of both modern regulatory and technological standards.
1. As-Built Surveys and Assessments
Unlike greenfield projects, brownfield work begins with detailed audits and assessments of the existing facility. Brownfield projects often involve working around pre-existing constraints such as limited space, fixed cleanroom classifications, and ageing HVAC systems. Fabtech assesses the current layout, structural integrity, process bottlenecks, utility capacities, and regulatory non-compliance. Based on these findings, we determine what should be retained, repurposed, or replaced, ensuring continuity with minimal disruption.
2. Compliance Retrofitting
Retrofitting for regulatory compliance is a key strength. Fabtech helps clients bring outdated facilities up to current GMP and international standards through intelligent redesign, cleanroom reclassification, HVAC system upgrades, and automation enhancements.
3. Phased Construction Planning
To ensure minimal downtime, Fabtech plans construction in carefully executed phases, working during off-hours or planned shutdowns. This ensures that new systems can be integrated without halting existing processes. This phased implementation approach ensures personnel safety and prevents cross-contamination in sterile and high-potency environments where any breach could affect product integrity.
4. Intelligent Integration
Strategic planning is crucial for integrating new equipment into the existing facility, considering space, utilities, and personnel flow. Fabtech handles equipment retrofitting, custom utility piping, electrical load balancing and process layout reconfiguration. Such integration requires not only engineering know-how but also cross-functional coordination with the client’s production and quality teams.
5. Safety and Risk Mitigation
Fabtech deploys cleanroom containment solutions, process segmentation, and sterility testing isolators to ensure operational safety during construction and system upgrades. Brownfield projects can pose unique challenges in terms of maintenance and operations. Thus, maintenance planning, training, and lifecycle management are also considered to future-proof operations.
6. Regulatory Compliance Upgrades
Older facilities often lag in current standards. Fabtech implements upgrades that include contamination control, automated systems with data integrity, and segregated material and personnel flows. These upgrades transform legacy plants into globally compliant, efficient operations.
Common Threads in Both Approaches
Despite their differences, greenfield and brownfield projects share a few foundational principles.
1. Client-Centric Collaboration
For every project, Fabtech closely collaborates with clients throughout the project lifecycle—right from user requirement specification (URS) and risk analysis to validation and handover. This approach ensures alignment of the facility design with the client’s process, market, and regulatory expectations.
2. Cross-Disciplinary Expertise
Both project types demand coordination across disciplines—civil, mechanical, electrical, automation, and process. Fabtech’s in-house multidisciplinary team ensures cohesive decision-making and agile problem-solving.
3. Sustainability and Efficiency Focus
Energy use, water management, and waste minimisation are increasingly important. Fabtech incorporates sustainable practices in both greenfield and brownfield contexts to offer heat recovery systems, clean air solutions like air handling units, and purified water distribution systems.
4. Validation and Documentation
Whether building anew or upgrading, Fabtech ensures facilities are built with validation in mind. DQ, IQ, OQ, and PQ protocols are built into the project plan, ensuring a smooth regulatory audit experience.
Real-World Applications
Fabtech’s expertise in both greenfield and brownfield projects spans geographies and therapeutic areas:
Greenfield – We have set up new oncology and vaccine manufacturing units in emerging markets like Nigeria, Algeria, and India, often with challenging timelines and high regulatory scrutiny.
Brownfield – We upgrade sterile production blocks in existing pharma plants without affecting daily output, especially in highly regulated markets in the Middle East and Southeast Asia.
The Fabtech Advantage
Fabtech is a global player in turnkey pharmaceutical projects, handling both greenfield and brownfield projects with tailored approaches through a blend of strategic thinking, technical expertise, and excellence in project execution.
Whether it’s a blank canvas or an existing plant, regardless of the starting point, the finish line is always made to perfection.
We don’t just build or upgrade structures, we build capabilities. Connect with us for end-to-end solutions for your next project.
Categories
Recent Posts
Subscribe
Never miss a post from Fabtech. Sign up to receive updates direct to your inbox.