The increasingly important role of RABS in aseptic filling operations
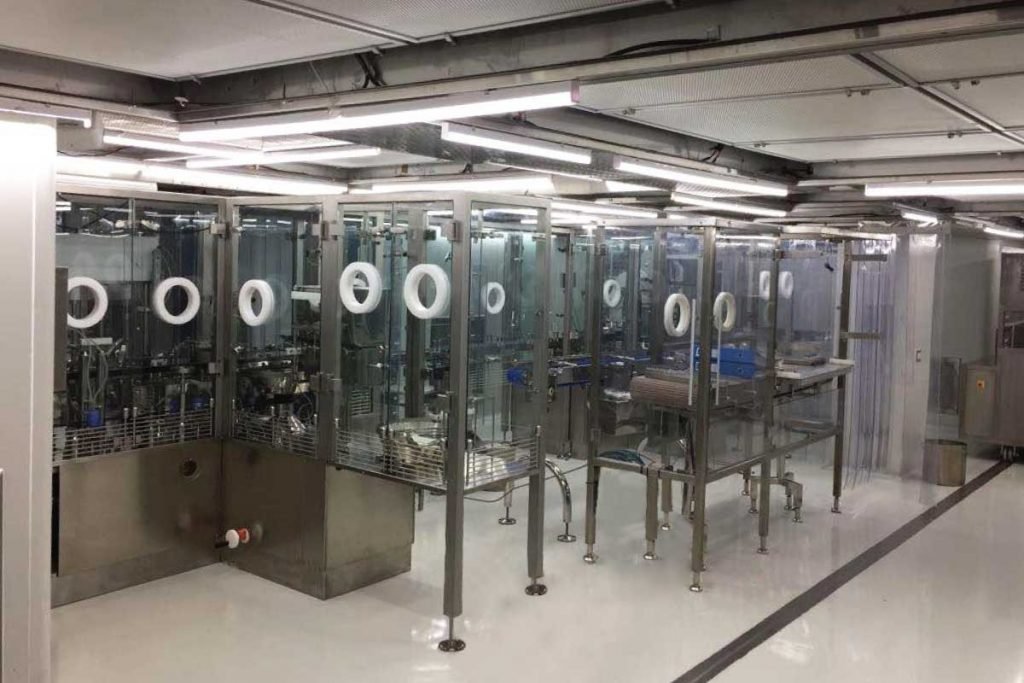
RABS is used in any industry where clean air is a requirement including pharma, chemical and electrical engineering. In pharma, while there are many advantages to using isolators in high-speed commercial manufacturing lines, for small-batch production of drugs RABS continues to be a flexible alternative. RABS is a welcome solution for existing cleanrooms to improve their filling quality and for any applications that require higher flexibility. RABS supports the achievement of the highest quality standards while offering additional operational flexibility. The key differentiator is that RABS can be an opened to allow for process intervention, while the isolators must remain closed during operation. RABS utilizes a physical barrier (both rigid and flexible barriers) and aerodynamics (air flow with filtration) to create an improved level of separation between the inside and outside of a defined volume.
RAB systems are broadly classified as
Passive open RABS: This system has no dedicated built-in air management system but utilises the surrounding cleanroom ventilation system for its airflow requirements. Air is filtered through the HEPA grid above the ceiling ensuring unidirectional airflow and is then released back into the ambient environment under controlled conditions.
Active open RABS: It has a built-in air management system that operates independently of the surrounding cleanroom ventilation system. The unidirectional airflow arrangement is mounted on top of the system. It sucks the ambient air out, passes it over the HEPA and the resulting unidirectional airflow is released into the ambient environment under controlled conditions.
Active closed RABS: This system has a dedicated air management system, that is entirely independent of the cleanroom ventilation system. Active closed RABS can be operated as a positive pressure system for product protection and negative pressure for operator protection. There is greater flexibility of control over design and operating parameter like temperature, RH and differential pressure.
At Fabtech, we employ RAB and containment technologies to provide the most suitable solution for manufacturing, filling and closing processes whether for non-potent or potent molecules.
While RAB systems are customised solutions to specific applications, the following design characteristics are built-in to every solution.
- Rigid wall enclosure and interlocking doors
- Ventilation system to ensure unidirectional airflow, and provide ISO 5 cleanliness levels and desired velocity at critical zones
- Appropriate decontamination (CIP/SIP) system for contact areas. Product contact areas are sterilised in moist steam steriliser and transferred to RABS per pre-defined SOP and assembled aseptically.
- Rapid transfer port to control the entry of materials into the RAB system under ISO 5 cleanliness standards.
- Glove ports, half-suits or appropriate automation to allow safe manipulation inside the RABS system. Gloves and half suits are sanitised to minimise the risk of contamination and leak tested per SOP before batch manufacturing.
- Appropriate decontamination mechanism to disinfect non-product contact surfaces within RABS before batch manufacturing. We recommend the VHP decontamination system.
- Appropriate localised classification of background environment around the RABS and properly designed material transfer points into RABS – liquid, stopper, seal etc
- Flexibility to allow for the remote occurrence of the door opening.
In the remote occurrence of the door opening, regulatory issues must be considered during operation to ensure there is no potential compromise of the aseptic environment that can prove hazardous. Appropriate measures must be taken to ensure the aseptic environment is maintained and there is no leak in the system.
While implementing a RABS, companies must follow a strict intervention protocol that includes sanitisation, line clearance recovery and restart with proper record keeping. Engineers and maintenance personnel must ensure proper maintenance.
Here are some key criteria to consider when selecting a containment solution
Manufactured at our state-of-the-art Umergaon facility, Fabtech’s RABS systems are fully automated, and PLC controlled with customised automation and data storage as required. All our systems are 21 CFR compliant with an audit trail.
If you would like more information on our RABS systems, please use the form below to get in touch.
Categories
Recent Posts
Subscribe
Never miss a post from Fabtech. Sign up to receive updates direct to your inbox.