Water Purification – The Sterile Sustainable System
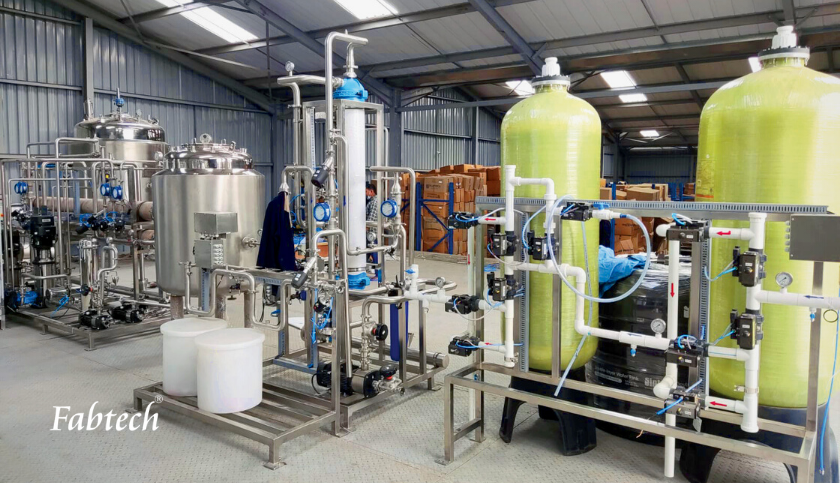
There is plenty of water on our planet; yet access to clean and pure water remains limited.
When we start to talk about pure water, a majority of us do not think beyond boiled water or the quintessential RO systems in our homes that give us direct access to purified drinking water.
But the essential fact is that 100% pure water doesn’t exist, and the processed water we get through ROs gives us roughly 90-95% more contaminant-free water than regular tap water. However, outside our homes, there are a myriad of industries that make use of ultra-clean water. Such industries viz. pharma, healthcare, food and beverages, cosmetics undertake stringent water disinfection and purification practices to set up an ultra-clean water system and carry out their day-to-day activities, production processes and other business purposes.
Infact, it won’t be wrong to say that absence of an efficient water system will not only adversely affect the industry alone, but can invite far-reaching implications on the health and safety of patients and users at large. This is what makes us, the life engineers at Fabtech come into the picture and assume our responsibilities towards the society.
Besides, by way of supporting our clients to establish a sustainable water system all over the world, we strive to transport our efforts towards global healthcare.
This blog will help you understand our high-purity water solutions to clients across various industries and sectors.
At the outset, let us discuss the distribution systems widely accepted in the pharma industry which play an integral role in the water system of the pharmaceutical industry. This is an automatic loop of operation that involves components and instruments which are designed to ensure further purification and maintenance of water quality. Programmable Logic Controllers (PLC) adhere to this distribution channel that controls the tank levels, loop piping velocity, temperature and conductivity. The loop primarily consists of a tank with two pumps that work directly or inversely with each other to maintain the loop pressure. The flow rate transmitter controls the pump’s frequency controller, which stabilises the pressure. The system is complemented with auxiliary elements such as overpressure valves, check valves, diaphragm valves, ultraviolet lamps and heat exchangers.
1. Purified Water (PW) Distribution System
In this system, the ‘pre-treatment’ modifies the supply of water quality until it becomes suitable for final treatment. Subsequent to the pre-treatment, water hardness, organic material, microbiological impurities, applied chemical agents, particles and turbidity are eliminated. There is also control over fouling, rust, corrosion, degradation and microbial growth. The final treatment is carried out wherein pre-treated water is passed through the reverse osmosis modules. The microbial load is further reduced by making the treated water pass through a UV lamp. The purified water is held at room temperature.
Dead legs in piping lead to water stagnation and eventual microbial growth and, therefore, due care is taken so that it doesn’t exceed more than 1.5 times the pipe diameter. The slope loop should also not be less than 10mm/meter so that complete drainage and microbial-free PW can be maintained throughout the system and at user points. The hold time must also have no leakage and drop in pressure.
Fabtech offers a wide range of advanced water purification systems with models ranging from 200 LPH (0.2m³/hr) to 20,000 LPH (20m³/hr) flow rate.
2. Water for Injectables (WFI) Distribution System
WFI, as the name and its usage suggest, is sterile and promises the purest chemical purity of water. The preparation of injection solutions involves a distillation, i.e. changing from a liquid state to vapour. The pure water that is produced through the distillation process is further passed through Multi Column Distillation Plant (MCDP). This plant works on the principle of heat exchange. The heating and cooling process is repeated in the distillation process, making the PW undergo a series of columns. The output thus obtained at the end of MCDP is the Water for Injectables.
This water is 100% pyrogen-free and is stored in a continuously circulating system, and is generally kept at 80 – 85 ºC to maintain its properties. The ability of this process to eliminate ionic materials, particulates, colloids and non-volatile organic compounds and bacterial endotoxins makes it the most accepted method for WFI.
MCD (Multicolumn Distillation Unit) + Distribution Systems works on an energy-saving design based on falling film technology with a working principle. In addition, the system includes an inbuilt sanitization mode responsible for maintaining the loop under sterile conditions.
With flow rates ranging from 80 LPH to 5000 LPH, Fabtech offers a customizable configuration and sleek construction of a combi-unit option for Pure Steam generation from the first still outlet of the WFI generator. Automatic/semi-automatic variants with 21 CFR Part 11 compliance with SCADA. Standard/reduced skids are incorporated in control devices and monitoring equipment for the WFI system. This systematic approach considerably reduces assembly time and provides optimum performance with a minimum footprint. Our high-quality orbital welding with boroscopy and videoscopy ensures efficiency by properly reviewing and inspecting piping surfaces and joints.
3. Pure Steam Generator (PSG) and Distribution
The system is used extensively for sterilizing vessels, viz. fermenters and filters, piping distribution system, autoclaves, and humidifying sterile rooms. Pure steam ensures that the system remains particulate-free by sterilising any equipment coming directly in contact with the sterile medicinal product. The operation is undertaken by the distillation process, where heat transfer occurs in shell and tube heat exchangers by falling film evaporation, thereby bringing in sterility.
Our PSG includes models with flow rates ranging from 50 to 1500 kgs/hour.
Fabtech’s sustainable closed-loop circulation ensures optimum water and energy recycling through heat sanitizing, softening, reverse osmosis and continued electrode ionization.
The plants have a sleek mechanical structure in SS316L with orbitally welded joints, video-boroscope, and electro-polished parts of less than 0.4RA, offering a variable production capacity of up to 80%.
The solutions meet the internationally recognized quality standards, such as USFDA 21 CFR part 11 and GAMP 5 compliant, with validation, FAT and test facilities.
We also provide operational and maintenance contracts and plant spares for seamless operations.
Categories
Recent Posts
Subscribe
Never miss a post from Fabtech. Sign up to receive updates direct to your inbox.