The benefits of intertwined circuiting in split coils
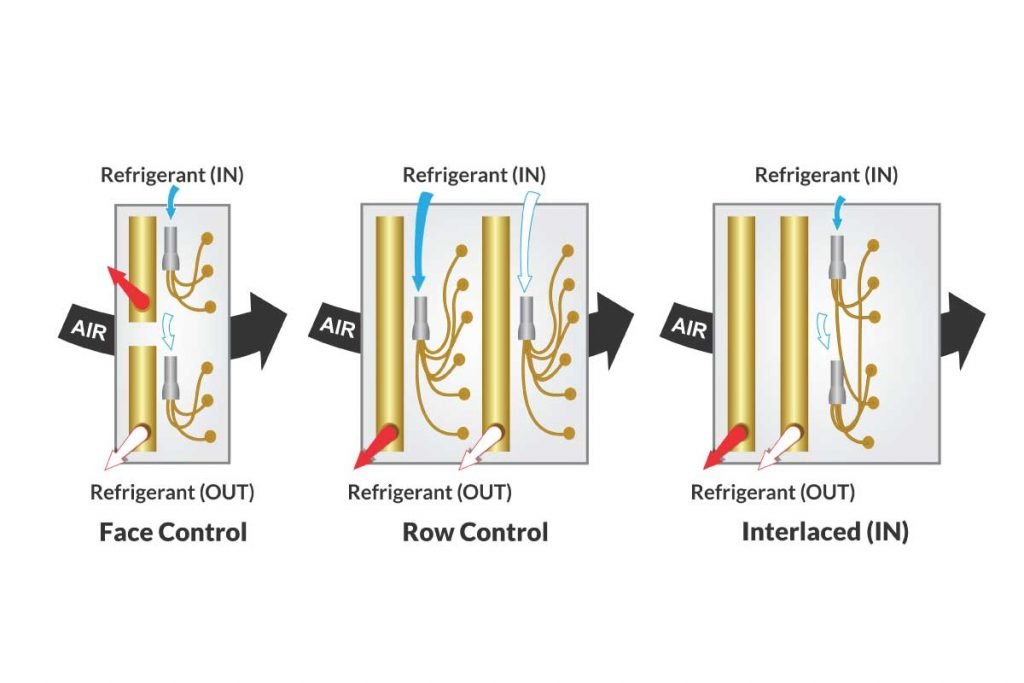
As most of these technologies and innovations are relatively unknown, we at Fabtech believe they need to be popularised so customers know to ask if for them as a standard operating procedure.
This post, which features Intertwined Circuit Coils, is the second in our series about sustainable engineering innovations championed by the HVAC sector.
In air conditioning, cooling systems come in two types – Direct Expansion (DX) and Chilled Water-type of central air conditioning plants. In DX systems, air used to cool the space is passed directly over the cooling coil of the refrigeration plant, while in the chilled water system, a refrigeration system first chills the water, which in turn chills the air used to cools the space.
Though both have their own advantages and limitations, since the air is cooled directly by the refrigerant in the cooling coil of the AHU, the cooling efficiency of DX plants is higher than chilled water plants. DX type of central air conditioning systems are generally used to cool small buildings or the rooms on the single floor.
DX evaporator coils are designed for use in air-side applications for cooling and dehumidifying. A relatively unknown technology is the splitting of the evaporator coil to match load changing demand, increase cooling efficiency and save costs. To split a coil, you put two complete and separate fin/tube coils in a single casing. By doing so, two compressors can operate off the same coil, and you can even shut one down when the load doesn’t require it. For example, if using a coil designed to give you 20 tons, and you split the coil, then two 10 ton compressors can feed off it simultaneously. However, if on any given day you require only half the full load, you can shut down one compressor entirely and operate the other at 100%.
To enable this, however, the coil needs a relatively unknown circuiting arrangement. There are three ways to split a coil. The first two – Face Split and Row Split are more commonly used, while the third, Intertwined Circuiting is relatively unknown. It is used far less than the other two methods as a result, but in terms of savings, it is highly cost effective in the long term.
Face Split
When you ‘face split’ a coil, a horizontal line is drawn across the front of the coil from left to right to divide the coil into the top and bottom halves. Each half is circuited individually resulting in two separate coils in a single casing. Individual compressors are then connected to the top and bottom coils. This method of splitting, however, comes with a significant disadvantage. As the air is directed across the front of the coil when the system is unloaded, air passes over the half of the coil that isn’t in operation resulting in air stratification
Row Split
To row-split a coil, it is divided into vertical rows with some rows in one circuit and the rest in the other. By doing so, though air passes across the entire front of the coil, it will always pass the rows in operation. However, it is challenging to get an accurate 50:50 split with this method. When aiming for an equal split on, say an 8-row coil, the top four rows closest to the air ingress take on a higher load than the remaining four. As a result, the coil is split 66:34 and not 50:50. You can try different permutations to ensure a 50:50 split, but doing so often results in a very complicated coil design to build and circuit.
Intertwined Circuiting
The best method of splitting coils is to intertwine the circuiting. In this method, alternate tubes are included in the first circuit and all the others in the second. So tubes 1, 3, 5 and 7 in the first row are combined with 2, 4, 6 and 8 in the second row to form circuit 1. Ditto for all succeeding rows. All tubes not in circuit 1, are included in circuit 2. The result is an interwoven mat of alternating tubes in the entire coil split into two independent circuits to feed into each compressor. Based on the expected load, each separate circuit needs a separate distributor and expansion valve. The design must also factor in total BTUs, refrigerant types, suction temperature and the number of tubes being fed.
The essential advantage of this method is that even though air passes over the face of the coil, there are always tubes operating if one of the compressors is switched on. The split is always precisely 50:50. This saves you energy and money.
Even more improved technologies are expected in the future as more and more companies intentionally employ an environmentally conscious approach to their design engineering.
If your next project calls for a split coil, make sure to ask for intertwined circuiting. Better yet, call us. We’ll come up with the most optimal way to circuit the coil and give you the best ROI
Categories
Recent Posts
Subscribe
Never miss a post from Fabtech. Sign up to receive updates direct to your inbox.