Precision Manufacturing: The Critical Role of Cleanroom Systems in the Semiconductor Industry
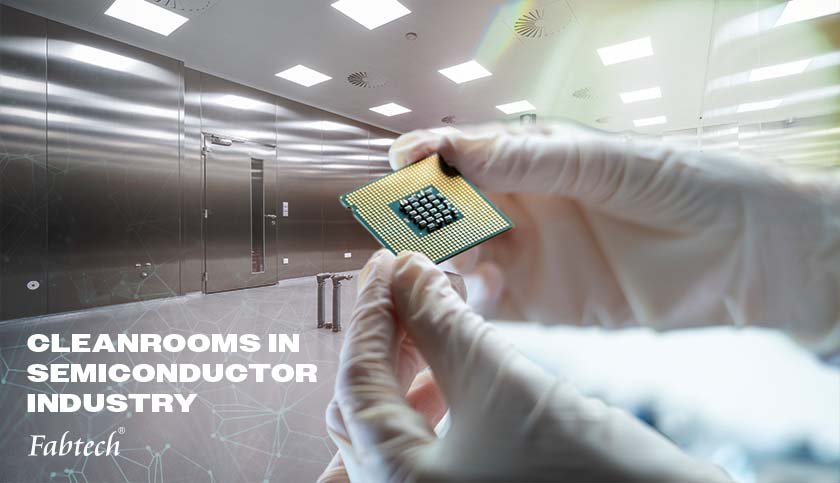
As you read this blog on your computer or mobile phone, numerous unseen elements in your device are actively performing their roles. Beneath these surfaces are semiconductors, playing a crucial part in ensuring the performance and reliability of operations and commands.
For instance, the silicon chips in our mobile phones must achieve optimum purity to function. Even the slightest imperfection can render a chip inoperative. Attaining this level of purity requires heating silicon until it becomes molten.
Beyond this, semiconductor fabrication involves many intricate processes. Collectively, referred to as “fab,” these processes transform raw materials into functional electronic components, with each stage requiring precise control and attention to detail.
Engineering equipment and technologies in semiconductor industries help create a sterile and controlled environment for manufacturing electronic components. In this blog, we shall explore the key roles played by them.
The Importance of Cleanrooms in Semiconductor Manufacturing
Cleanroom systems provide sterile and controlled environments essential for semiconductor manufacturing. These regulated spaces ensure optimal air quality, temperature, humidity, and other environmental factors, which are crucial for maintaining the high standards required in this industry.
Let’s learn the significant roles cleanrooms play in semiconductor manufacturing:
1. Photolithography:
Photolithography involves transferring patterns onto a semiconductor wafer using light. Contamination can distort these patterns and cause defects. Cleanrooms maintain a particle-free environment, ensuring the integrity of photomasks and photoresist layers. High-efficiency Particulate Air (HEPA) and Ultra-Low Penetration Air (ULPA) filters remove airborne particles, ensuring stringent air quality standards.
2. Etching:
This process involves chemical procedures to clean wafers and create precise circuit patterns. Cleanrooms prevent airborne particles from interfering with this process, ensuring the accuracy and consistency of the etching process.
3. Wafer Processing:
A silicon wafer is a thin piece of material that serves as the foundation of semiconductor devices. During processing, wafers must remain free from particles that could cause defects. Cleanrooms control the temperature and humidity levels to prevent environmental fluctuations. They thus provide an environment with minimal particulate matter, ensuring high-quality wafer production.
4. Mask Making:
Masks used in photolithography to transfer circuit patterns onto wafers must be produced in a contamination-free workspace. Cleanrooms maintain precision for accurate pattern transfer, eliminating the risk of defective patterns on the wafer.
5. Deposition:
Deposition processes, such as chemical vapor deposition (CVD) and physical vapor deposition (PVD), involve placing material layers on wafers. Cleanrooms ensure uniform and consistent, defect-free material layering by preventing airborne particles from settling on the wafer and maintaining the purity of chemicals and gases in deposition processes.
6 . Cleaning:
Cleaning processes remove residues and particles from wafers while ensuring that the cleaning agents and methods meet the stringent standards of semiconductor manufacturing. Cleanrooms enhance the effectiveness of these processes by providing an environment where recontamination is minimized.
7 . Testing:
Testing semiconductor devices for functionality and reliability requires a contamination-free environment. Cleanrooms ensure that test results are not compromised by external particles. With this sensitive equipment protection, cleanrooms ensure equipment’s efficiency, accuracy, and longevity.
The Role of Cleanroom Panels
Cleanroom panels are more than mere walls, playing a vital role in regulating environmental conditions within a cleanroom. Below are some key aspects of their crucial role in semiconductor manufacturing:
1. Contamination Control:
Cleanroom panels prevent contaminants such as dust, airborne microbes, and chemical vapors from entering the manufacturing area. This prevention is essential in semiconductor manufacturing, where even the smallest particles can cause defects.
2. Air Filtration:
Cleanroom panels work with high-efficiency particulate air (HEPA) filters and ultra-low penetration air (ULPA) filters to maintain a constant flow of clean air. This conjunction helps remove any particles generated during the manufacturing process.
3. Durability and Cleanability:
Fabtech’s pre-painted galvanized iron (PPGI) cleanroom panels are constructed from durable, easy-to-clean materials that ensure high cleanliness standards, add robustness, and resist corrosion and degradation. Their longevity and resistance to scratches and chemicals reduce the need for maintenance, replacements, and repairs, even with regular cleaning.
4. Modular Cleanroom System:
Modular cleanroom panels allow for flexibility in expanding or reconfiguring cleanrooms as needed. The panels are interconnected with aluminum profiles, making for sturdy assembly and a robust cleanroom system. Disassembly or replacement of a single panel can be carried out without disturbing other panels, and rooms can be resized as needed. The adaptability of modular cleanroom wall systems is beneficial for accommodating changes in manufacturing processes or scaling up production.
5. Standardized Material:
Mineral wool, an insulation material is approved by global regulatory bodies and offers higher fire resistance up to 500°C and a better fire control mechanism for up to 120 minutes. The wall panels are also tested by FM approvals – a legitimate, qualified body recognized for certifying property loss prevention products.
6. Environmental Stability:
Cleanroom panels help maintain consistent environmental conditions by providing superior control over airflow, temperature, humidity, and filtration. Stability in these conditions is vital for precision manufacturing processes. For instance – PPGI cleanroom wall panels are energy efficient and contribute positively to the indoor air quality of cleanrooms.
7. Seamless Integration:
Cleanroom panels integrate with other cleanroom components such as doors, windows, and pass-through chambers, ensuring a cohesive and effective barrier against contamination. Profiles are concealed to avoid leaks. Wires and conduits can be passed from within the panel.
Semiconductor manufacturing involves handling hazardous chemicals, which pose potential health risks to operators. An intelligent cleanroom system is essential for creating a controlled environment that ensures both the safety of workers and the high productivity and reliability of the final products.
As technology advances, semiconductor fabrication processes continue to evolve, enabling the creation of powerful, high-performing devices that will drive the future of the electronics industry. From microprocessors, and memory chips to advanced sensors, cleanrooms remain critical for maintaining accuracy and meeting the stringent demands of modern technology.
Fabtech, with its extensive portfolio in cleanroom applications, understands the growing needs of various industries, including pharmaceuticals, healthcare, and semiconductor manufacturing. We help you build cleanrooms that are not only paramount but also foundational for the powerful functioning of future technologies.
By partnering with Fabtech, you gain access to expertise in designing and constructing state-of-the-art solutions for cleanrooms tailored to your specific requirements. Our clean-air solutions ensure that your manufacturing processes remain at the forefront of industry standards and continue to support cutting-edge technology development.
Categories
Recent Posts
Subscribe
Never miss a post from Fabtech. Sign up to receive updates direct to your inbox.