Paving a Pyrogen-Free Passage through Sterilising & Depyrogenation Tunnels
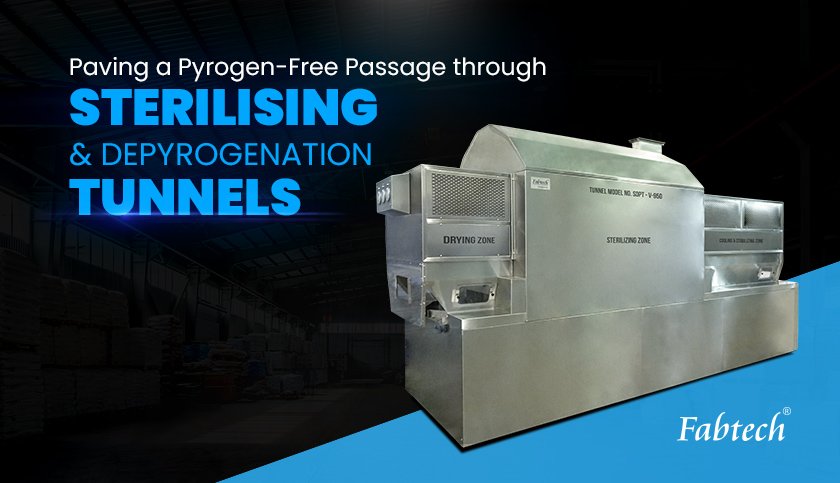
There is a striking similarity between the acts of caring for a baby and treating a patient. Both are vulnerable to infections and so require extra care and attention. Just as a baby’s family carefully uses sterilized bottles for feeding, similar meticulous care goes into providing patients with sterile treatment.
However, when it comes to treatments like vaccinations or injections, hygiene is equally crucial for all of us to prevent any kind of contamination.
Among the many factors that contribute to the sterility of the injections and vaccines, sterilizing and depyrogenation tunnels are important equipment used in pharmaceutical and biotechnology industries. This equipment is specifically designed to ensure optimum removal of pyrogens from containers, vials, ampoules, or other products before filling them with sterile substances. Pyrogens that can cause fever when introduced into the body need to be crucially removed to avoid any adverse reaction in patients. These tunnels play a critical role in upholding the quality and safety of injectable medications, vaccines, and other sterile products.
The removal process is carried out by utilizing heat, typically dry heat or hot air, to kill or inactivate microorganisms like bacteria, viruses, and fungi, rendering the items passing through it sterile. The process is essential to prevent contamination of pharmaceutical products and maintain their efficacy and safety.
What are the techniques?
There are two main techniques used for depyrogenation – batch and dynamic.
Dynamic Depyrogenation
Dynamic depyrogenation involves the use of a sterilising-depyrogenation tunnel where products are transported over a continuous band through the different heating zones of the tunnel. The pyrogens are effectively removed along the operation and the final product, free from fever-inducing substances, is achieved.
Batch Depyrogenation
As not all products can withstand the high temperatures required for the depyrogenation process, batch depyrogenation is carried out in static ovens, especially for metal containers and heat sensitive solutions where the products are placed in metal crates and exposed to high temperatures for a specified period. The process helps in deactivating and removing the pyrogens from a specific batch.
How do they operate?
- Containers or products are loaded onto a conveyor belt or trays.
- The items are passed through the tunnel, where the heat is applied at a set temperature and exposure time to achieve effective sterilization.
- After passing through the tunnel, the containers become pyrogen-free and achieve sterilization, ready to be filled with sterile substances.
How are they useful?
Sterilizing and depyrogenation tunnels offer several advantagesin the pharmaceutical and biotechnology industries, where maintaining product sterility and removing pyrogens are of paramount importance. Here are some of the key advantages of using these tunnels:
Enhancing Product Safety – In the pharmaceutical industry, product safety is of utmost importance. Sterilizing and depyrogenation tunnels provide a reliable and validated method to eliminate or inactivate harmful microorganisms and pyrogens from pharmaceutical containers and products. By ensuring products especially injectable like vaccines and medication are sterile and free from pyrogens, these tunnels significantly reduce the risk of infections and adverse reactions in patients, thereby enhancing product safety.
Quality Assurance – By providing a reliable and validated method of sterilization and depyrogenation, these tunnels contribute to maintaining consistent product quality. The processes carried out in these tunnels are carefully controlled and monitored, leading to reliable and reproducible results.
Reduced Contamination Risks – Contamination is a significant concern as it can compromise patient safety. However, the enclosed design of the tunnels minimize the risk of contamination during the sterilization and depyrogenation processes. The controlled environment helps maintain aseptic conditions and prevents any external contaminants from entering the system.
Process Integration – These tunnels can be seamlessly integrated into automated pharmaceutical manufacturing lines. This allows for continuous processing, thereby streamlining the pharmaceutical production process and reducing the need for manual interventions and minimizing the chances of human errors, thus contributing to increased productivity and throughput. This nature of sterilizing and depyrogenation tunnels ensures that the processes are repeatable and reproducible. This consistency in results is crucial to maintain product quality and avoid batch-to-batch variations.
Versatility and Adaptability – Sterilizing and depyrogenation tunnels can be used for a wide range of products and containers, making them a versatile equipment. These tunnels are designed to handle and accommodate different types of vials, ampoules, cartridges, syringes, and a large number of containers or products of various kinds and sizes in a continuous manner, making the sterilization and depyrogenation processes efficient and time-saving and contributing to improved overall manufacturing efficiency.
Compliance with Regulatory Standards – Pharmaceutical industries are subject to strict regulations and guidelines, especially concerning product sterility. Sterilizing and depyrogenation tunnels offer a standardized and validated approach to meet the required sterility and pyrogen removal standards, ensuring compliance with regulatory requirements.
Cost-effectiveness in the long run – While initial investment in these tunnels may be significant, their long-term benefits of reducing the likelihood of product recalls due to contamination and ensuring compliance with regulations, make the equipment cost-effective.
Validation and Documentation – Sterilizing and depyrogenation tunnels are subject to extensive documentation and rigorous validation procedures to ensure their effectiveness and reliability. The validation process provides documented evidence that the equipment consistently meets the required standards, enhancing process control and traceability of the sterilization and depyrogenation processes.
What is the qualification process?
The qualification process and its requirements are as follows:
Installation Qualification (IQ)
- The tunnel and conveyor belt must be at least 304 stainless steel.
- The unit is supplied with heat resistant HEPA filters.
Operational Qualification (OQ)
- Critical Areas should have laminar airflow of 90 fpm ± 20%, or 28 m/min ± 20%
- The tunnel must meet specifications for total particulates for a Class 100 area.
- Rate of speed (minimum, maximum and nominal) is measured and verified.
- Physical handling of containers is monitored.
- There should not be any dislodged or damaged containers.
- The tunnel is temperature mapped to demonstrate consistency.
Performance Qualification (PQ)
- Vial size that will be used during production will be qualified.
- Temperature uniformity and delivery of heat will be documented.
- Tunnel differential pressure during the depyrogenation period is monitored.
Sterilizing and depyrogenation tunnels are an essential pharmaceutical process equipment, providing modern and high-quality solutions to several pharmaceutical challenges. The product offers an efficient and reliable approach to address critical challenges, ensuring the safety of pharmaceutical products for patients.
In keeping with our long-standing endeavours of saving lives through turnkey pharmaceutical engineering projects, equipment and solutions, Fabtech sterilising and depyrogenation tunnel demonstrates our continued commitment in achieving effectiveness through optimum sterilization. Our fill and finish solutions encompass production and packaging lines for parenteral and sterile liquids in vials, ampoules and prefilled syringes. Our equipment viz. prefilled syringe machine, vial filling and capping machine along with sterilizing and depyrogenation tunnels offer an end-to-end solution for your project.
We would like to learn more about your project requirements so that we can tailor-make and offer you the best solutions that will benefit your project and ultimately help serve people better.
Categories
Recent Posts
Subscribe
Never miss a post from Fabtech. Sign up to receive updates direct to your inbox.