Things to be taken care while designing a cleanroom
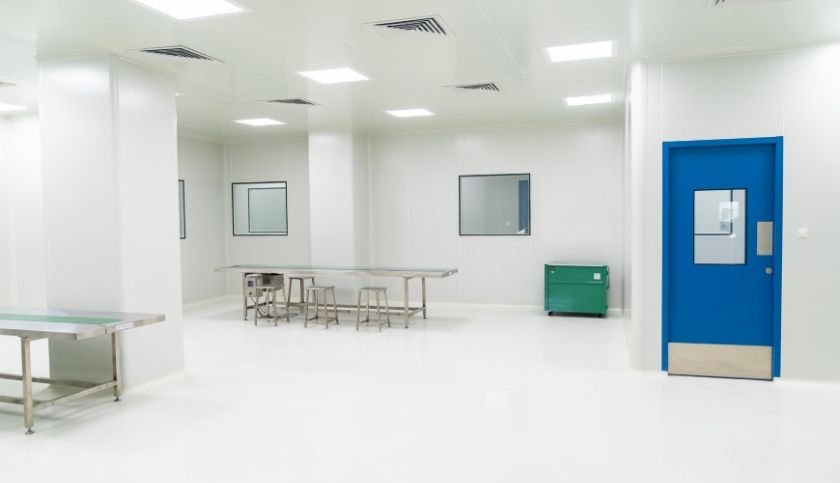
Cleanrooms facilitate quality output as they provide clean air and a controlled environment. Every new cleanroom project we undertake offers us a unique set of challenges. We recently visited a biotechnology customer’s facility, where we pitched for biotechnology cleanrooms. Though the customer seemed eager to get started on the project with us, he had a common yet pertinent question – why he should choose us over the other cleanroom manufacturers, including the existing one who had worked on his previous project.
It is a given for any cleanroom manufacturer to focus on the design aspects of the cleanroom. Hence I realised the need to cut through the clutter and wanted the customer to sense the uniqueness of Fabtech. But how?
A cleanroom design may seem following the ISO or Good Manufacturing Practices, yet it may have flaws that may lead to contamination. As a part of Fabtech Technologies, a well-known engineering solution provider for Pharmaceutical, Biotechnology, and Healthcare, I want to focus on design flaws and critical parameters, if neglected, may lead to non-compliance in manufacturing a cleanroom facility. I thought of putting together cleanroom practices that may still be a part of the cleanroom process; however, it may not be relevant anymore.
Fig. 1 | Particle deposit and Metallic Particle or Hurdle
Let us begin with HVAC systems and its workings, the heart of a cleanroom. Let’s assume that we have one room connected to one AHU that maintains the flow of air in the room through supply ducts and supply grills and return riser to return duct and back to AHU. This airflow pattern is designed setting a minimum number of air changes per hour (suppose 30 ACPH) as per the defined criteria for maintaining a particular class (class D).
The above figure demonstrates the cleanroom airflow pattern, maintained as per the APCH in the room. However, any hurdle, or metallic part of the equipment not included in SOP under cleaning and maintenance after every batch change over, create an opportunity for dust particle accumulation. As deposition increases with time, it comes in circulation in the next batch of products leading to cross-contamination.
Not only is this harmful, but contamination of the dust particles in coming in contact with the new batch of products may become fatal in some cases. Further, if not removed, dust in combination with moisture result in microbial growth, again a significant non-compliance, and may test positive for swab test conducted by the microbiology department.
Prevention is Better Than Cure:
The pharma manufacturing industry has long realised that ‘Prevention is better than cure.” The design parameters for cleanroom equipment and accessories should focus on the impediments that may cause contamination (in short prevention). We are referring here to the immobile elements of the cleanroom. The QA department prioritises cleanroom cleaning procedures, including cleaning and changeover, for movable parts, like the machinery, etc.
I am restricting the scope of this article to focus on cleanroom accessories and immobile parts. In my opinion here are a few points to be taken care of while designing a cleanroom:
- The corners and covings of a cleanroom should not have sharp-edges. The use of curved and non-edgy accessories devoid of sharp edges prevent dust accumulation.
- The mechanical components of a cleanroom, especially in computer and electronic industries, i.e., wafer-processing environment, contribute to contamination. The surfaces of the parts should be smooth, contain fewer joints for cleaning.
- Utilities or equipment must be surface-mounted to the floor or flush mounted to the plane of a wall. This will provide for easy cleaning corners within the cleanroom
- The surface should free of ledges and not break up, peel off or chip off easily that generates dust particles leading to contamination. We have elaborated this in one of our earlier cleanroom blogs – the advantages of modular over traditional construction for pharmaceutical cleanrooms. (can we add a link to the blog)
- Screws, rivets, butts, and joints, or any protruding components, should be avoided or kept to a minimum (can be sealed with silicon) on the walls or ceiling of the cleanroom.
- Utility services like electric wires to be concealed with the use of in-built conduits to avoid any cables or pipes hanging in the facility.
- Flush-fitted double glazed view glasses may be used to avoid any dust or particle accumulation around them.
- Light electrical fittings like smoke detectors, wall-mounted phones, internet connection, switch boxes, all should be either flush-fitted or have a curved surface easy cleaning and reducing contamination.
- The wall guard is crucial to avoid damage to the metallic modular walls. Although it is essential, if floor-mounted, it may cause dust and microbial growth within the cleanroom facility. However, if it is wall-mounted, this can serve a dual purpose of easy cleaning and safety to panels.
Apart from this, the quality of the skilled engineering team is also very crucial to give on-site finishing to the sealant filling and fitting of grills and light fixtures, as these are points that are not in control at the manufacturer end but at the execution end.
To conclude, I would like to emphasise that, why wait for a disaster to strike when we can take steps to avoid it. The above pointers may help create a better SOP for the cleanroom facility.
Categories
Recent Posts
Subscribe
Never miss a post from Fabtech. Sign up to receive updates direct to your inbox.