A Day in the Life of a Project Manager – Part I
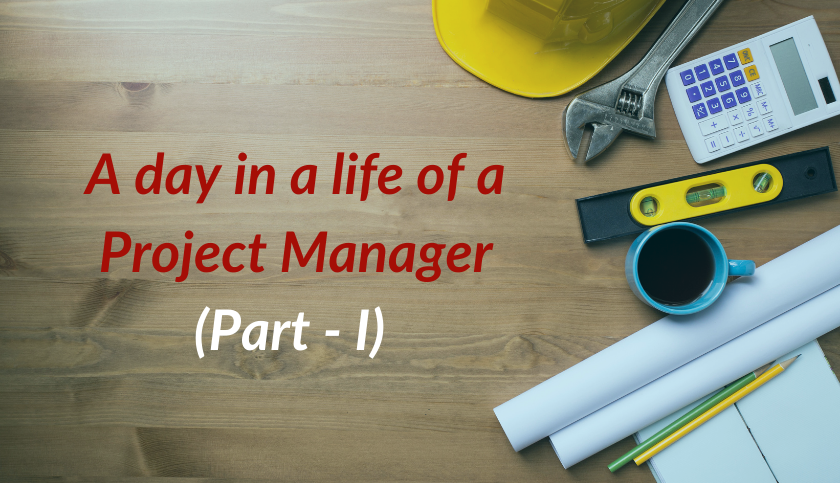
Real-Life Skills or self experiences can be truly enriching, better than classroom teaching! That said, traditional classroom learning is certainly beneficial. I can especially vouch for many engineering faculty professors, sharing their learnings and experiences with the future generation of engineering talent. But if there is one person I remember distinctly, it is a fellow student (Eng. Saff’aa) from Iraq whose words have etched in my memory, “Engineering is Economy. And If I were to dedicate this article, it would certainly be him.
THE INCEPTION:
It has been almost two years of employment with Fabtech Technologies, a company that builds Pharmaceutical & Biotech capabilities. Our vision is to build manufacturing capabilities so everyone has the same access to affordable life-saving medicines.
Building Manufacturing capabilities come with real engineering challenges and often does not have straightforward solutions. As a regional manager for the West African region, I encounter numerous challenges. In a nutshell, it is the shortage of available time and quality material to execute a modification.
THE FIRST CALL:
The first call I received was from a customer and a friend in Lagos (we shall refer him as Mr B henceforth). He expressed his concern over an HVAC system validation they were carrying out for an MNC. It failed to achieve the required relative humidity for one of his company’s most important technology transfer projects. I promised him to look into the matter, not only as a partner for providing validation services for Mr B company but, more importantly, as a friend in distress who was reaching out for guidance.
Having more than a decade of designing and executing HVAC systems for numerous applications, including cleanrooms, food processing, and comfort applications, I can comfortably say that it is tricky to resolve concerns over a phone call or video conferencing. It would help if you had your Engineering Hat on, rather than depending on technicians (even though they may be skilled), a piece of advice, especially for new Engineers to hold onto.
A Class ISO-8 Cleanroom measuring 25 square meters (See figure -1) and the original HVAC System comprised of AHU containing Mixing Box, Chilled Water-Cooling Coil Section, Filtration Box, Terminal HEPA Filters. Additionally, a Descent Dehumidifier to handle the latent load.
The systems designed on paper seemed flawless; however, in reality, the systems were unable to achieve the required relative humidity (as the designer had set that it should not exceed 45% due to the product’s hygroscopic nature). The humidity was fluctuating between 50-55%.
Here the relative humidity did not go according to the design while the installed dehumidifier is in operation. The first engineering question we addressed was whether the dehumidifier is working to remove the humidity? To answer this question, we measured the supply air parameters in contrasting situations: when the dehumidifier is on, and when it is off.
The results are displayed below:
Figure 1: Clean Room Layout
Figure 2: Original HVAC System
Parameters | Dehumidifier is on | Dehumidifier is off |
Supply air temperature | 20.4°C | 17.5°C |
Supply air relative humidity | 45.1% | 85.1% |
Supply air Humidity ratio | 6.76 g/kg | 10.72 g/kg |
It is evident that although the dehumidifier was working, it was not as per the desired level of performance. The room latent load calculation (generated from people and infiltration) gives us a 1.45 kW of latent load. Accordingly, the supply air humidity ratio should be at most 6.72 g/kg.
The next step was to probe the technicians. And as luck would have it, I got to probe them when their superiors weren’t around. This certainly helped as they were candid and straightforward. It threw light on the system usage, which wasn’t used from the day of installation till almost six years. While the system was unused for that period, the manual dampers were kept open, a common mistake of developing nations’ pharma companies. However, the ISO and the WHO have clearly specified that companies should keep all systems on other than periodic maintenance. Yet, this error is bound to occur when companies attempt to reduce production costs, pardonable in many cases.
What makes this case unique is it costs the company a complete dehumidification system. Decent dehumidifiers depend on a disc containing a hygroscopic material (mostly Silica Gel) to absorb the humidity out of the air passing through it. The Silica Gel’s hygroscopic ability is renewed by drying the disc using a stream of hot air passing through a different section of the disc that helps it works for a longer period. (Review figure 2).
However, In Mr B’s case, the disc was out in the open for nearly six years in Lagos, where the humidity levels are high (the relative humidity range over the year is 55 – 90 %). Hence it was fair to assume that the disc containing silica gel was saturated with water and required a replacement.
Although Mr B seemed bothered by this discovery, knowing that he was an able manager, it was easy to foretell what would our discussion be. He wanted a quick and economical solution.
Although I had a concept, I required more data. I required his team’s cooperation, and my request was accepted. The data helped me in concluding how the supply air parameters should be as the following:
- Supply air temperature: 13.3°C
- Supply air relative humidity: 72.6%
- Supply air Humidity Ratio: 6.72 g/kg
Here, I compare the parameters measured between the first experiment and this one, and it painted a clear picture.
It was simpler to keep the dehumidifier on as it accomplished the objective to reduce the air’s humidity level, despite its underperformance. However, I was surprised at the unusual surge in its temperature. Ideally, it should have been 13.3°C while it read 20.4°C, posing more questions than answers.
RACKING OUR BRAINS FOR THE SOLUTION:
The international company’s apparent solution was installing a new machine to increase the cooling load required from the AHU. And that was the first step in our plan, i.e. the addition of cooling capacity to reach the required air temperature. Another advantage of adding the cooling coil is the additional apparatus to dehumidify the room’s air, which works as a proper solution to reach the required air temperature supply.
TAKING A BREAK CAN LEAD TO BREAKTHROUGHS
I am sure you have a question about how did we achieve this? We have divided the blog into a two-part series. We hope you enjoyed reading PART I. Part II of this series will focus on how we achieved a breakthrough in solving the problem.
Categories
Recent Posts
Subscribe
Never miss a post from Fabtech. Sign up to receive updates direct to your inbox.